

Case Studies
23/04/2018 "significant reduction in lost time and minimal customer complaints" 20/02/2018 Reduce coat weights by 40% 19/02/2018 Reduced downtime from 6.09% to an average of less than 1% 10/07/2017 "Your support ...has been outstanding!" 26/06/2017 "I wasn't expecting to see a big difference, how wrong I was!" 22/06/2017 "257% increase in production speed" 17/05/2017 "35% reduction in consumption" 11/05/2017 "Unmatchable quality and consistency""significant reduction in lost time and minimal customer complaints"
23/04/2018A leading producer of personal hygiene products wrote in with this extremely positive feedback
"As discussed on your recent visit to the plant I would just like to pass on my feedback to you regarding our experience with your product and what it is doing for us as a business.
Since the introduction of your product on our case erectors we have had no issues or complaints from any of our customers in relation to case integrity and strength of adhesion. This was an issue prior to switching to Alphabond, so now that we are a fully established in this glue the yield and consistency remains as high today as when we started.
We have introduced lidded product into the market and in our early days we were in a different glue system. While working with you we have not only been educated and shown the possibilities of your product, but also, and very importantly you have a listened to our needs and the needs of our customers which allowed us to trial your product over a couple of months.
The report and presentation that you generated allowed me to lead the business alongside our Quality Manager and Engineering Manager into changing our glue offering.
We successfully launched into the FastLock system and we have expanded this to each of our robot machines. We have seen significant reduction in lost time and minimal customer complaints now we are in the new glue.
One of our challenges was shipping product to Australia, the original glue was proving to be a problem and we were seeing some bonding issues. After trials and testing we have not had a repeat of this issue since, and the customers are extremely happy with the improvements.
So to sum up, we are very happy, with the quality of your product, the consistency and the technical support we receive. We look forward to building this partnership more in the future."
Reduce coat weights by 40%
20/02/2018This company has been working with Alphabond for a number of years now and we constantly provide them with the latest technology to improve their Triple-P (Productivity, Presentation and Profitability).
The Packaging Manager on site gave us this positive feedback after a period of being on the new Perfecta MAX adhesive and validating the benefits we offered.
The Perfecta MAX has allowed us to reduce coat weights by ~40% and completely remove angel hairs and adhesive build up on belts post case erector. I would recommend Perfecta MAX to anyone using automated packing lines where cleanliness and GMP is important.
Reduced downtime from 6.09% to an average of less than 1%
19/02/2018We have worked with this customer for a long period of time now and being a multinational alcoholic beverages company, productivity and performance are paramount for them. When we asked the guys who work with our new adhesive on the production line day-to-day what their feedback was, they came back with...
During the focussed improvement project on the Taxomat we reduced downtime from 6.09% to an average of less than 1% sustained for a full year after the completion of the project. The biggest contributor to this was the change in glue.
"Your support ...has been outstanding!"
10/07/2017When we first met this leading food manufacturer they were buying a competitors product - which worked. But the client was keen to see if Alphabond could generate further cost and efficiency savings.
Trials of our Fastlock Perfecta MAX 24 grade were initially run on a box sealer, alongside an identical trial of the competitors original grade. The result?
- Notably less stringing/webbing with Perfecta Max, slashing the amount of housekeeping required on the machines
- Reduction in compression/glue set time from 4 seconds to just 1.5 seconds - enabling the customer to increase the throughput of boxes on the sealer with far less backlog
- Zero reports of poorly sealed boxes
- 30% reduction in coat weight
As a result of the success of this trial, the client converted all their lines to Alphabond saving thousands of pounds through efficiency gains.
"I wasn't expecting to see a big difference, how wrong I was!"
26/06/2017After using the same adhesive supplier for years, this brewing and packaging company assumed that all adhesives products were the same. In fact, they weren't expecting to see much improvement at all when we approached them with a better solution. But we don't believe the doubters, we prove them wrong!
After a free site audit, the customer agreed to trial our LabelLock® grade adhesive. Here are just a few of the incredible results they observed:
- Better label application across all products - huge reduction in winging labels
- Much easier to clean labeller, pallets and all parts during production
- Massive increase in labeller efficiency
- Glue usage slashed
- Happier operators all round!
With results like these, the customer was delighted to swap to Alphabond. Our relationship continues to this day.
"257% increase in production speed"
22/06/2017Line speeds of 14,000 pcs per hour were the norm for this well-known packaging company. But time is money on folder gluer machines. Every converting manager wants to eke out a little extra speed.
Often, the bottleneck in production is the adhesive. Machines cannot run at their full capacity if the setting speed of the adhesive does not allow them to. Ironically, because production time is so valuable, many managers are hesitant to trial a new product without a compelling reason to do so. When Alphabond suggested that their new Perfecta® Max 40 grade would enable line speeds of up to 30,000 pcs per hour, more than twice the current speed, the potential benefits were too great to ignore. A trial was quickly arranged.
In the event, the results were even more dramatic than projected. Line speeds were temporarily ramped up to 50,000 pcs per hour still giving good fibre tear and without excessive tailing. That's an amazing 257% increase-saving thousands of pounds in efficiency gains and giving the client a major advantage in the competitive world of packaging.
"35% reduction in consumption"
17/05/2017When a leading UK recipe products manufacturer needed to reduce waste and improve glue labelling efficiency, they turned to Alphabond. Through site visits, sampling and extensive lab tests we were able to recommend the use of LabelLock® 705 on their machines, a formula specifically designed to improve the "grab" specification of the glue.
The results were immediate and obvious:
- Excellent and consistent performance across various ambient temperatures
- Transfer of adhesive to non contact parts of the machines was virtually eliminated, massively reducing clean-down times
- Elimination of label slippage, slashing label wastage due to misapplication
Better still, the client got by on far less glue ... delivering a 35% reduction in consumption.
"Unmatchable quality and consistency"
11/05/2017After using the same old grade of adhesive for years, this bakery manufacturer assumed that regular nozzle blockages were unavoidable for hot melt adhesive. Production rubbed along until a serious case of pop-opens convinced the engineering team to look at alternatives.
After calculating the potential savings, the customer agreed to trial our Perfecta® grade adhesive. The superior heat stability was immediate and obvious. Nozzle blockages and charring were eliminated overnight with substantial improvements to clean-down time. There were virtually no pop opens from blocked nozzles. Better still, the client got by on far less glue-delivering a massive 28% consumption savings.
Since switching to FastLock Perfecta® 3P, the benefits have become even more apparent. The adhesive has proved versatile enough to cope with all board materials and at different line speeds. The outstandingly high tack has enabled operators to reduce the amount of adhesive applied; consumption savings are still being made. Over time, the exceptionally clean running, low-odour formula actually purged the hot melt systems clean, reducing downtime, reducing spend on spare parts and boosting production output for an instant hike in profits.
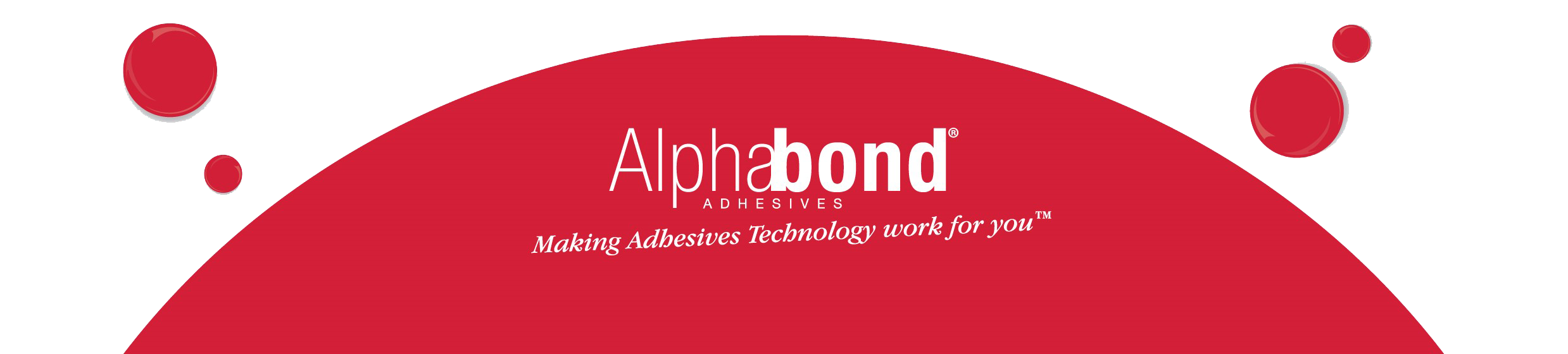